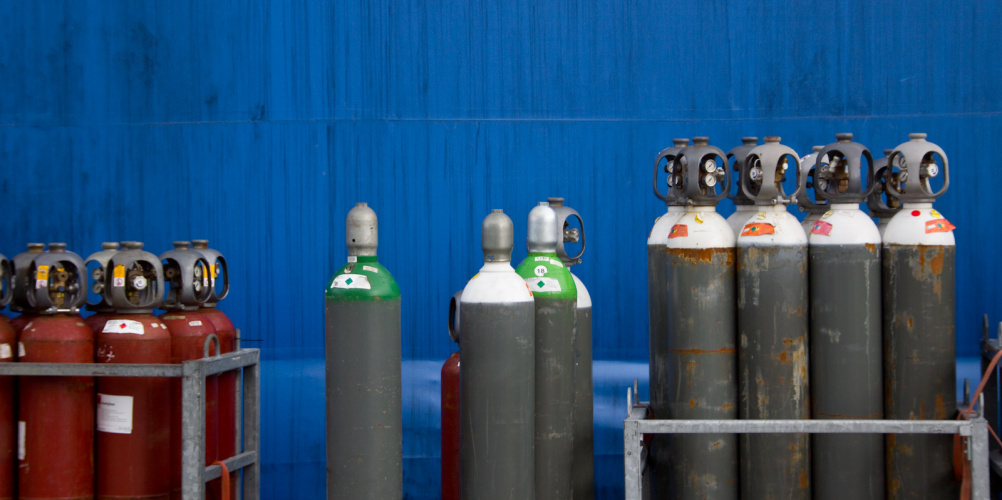
Field Service Operations using NFC
A leading provider of compressed gases was interested in improving field service operations using NFC Tags and backend software.
A leading provider of compressed gases was interested in streamlining their field service operations with the use of smart markers. By including some type of marker scannable with a smartphone, the company could increase productivity and reduce errors in field service processes.
They evaluated both NFC Tags and QR codes and decided on NFC tags because of the rugged environment that canisters were used in and the possibility that canisters would be facing in a direction where camera access could be too difficult or have insufficient lighting. For tags on a metal cannisters they decided on using larger tags with a ferrite backing to improve communications and read distance.
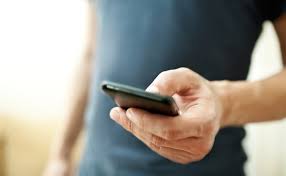
The experience the company created was a front end to their existing field maintenance software that would let the field service technician record maintenance activities and fill rates in certain conditions. By using NFC and connection software, the date, time, and location were defaulted into every interaction and the user was defaulted from the phone being used. With the use of drop-down menus for any operations performed, errors were reduced to less than 3%.
The company increased the efficiency of field service technicians, allowing for more site visits per technician. The speed of communications with the base field service software gave leadership a real time picture of field operations and the status of individual cannisters and installations in the field.
Tapwow Takeaways
- Choosing the right marker for a given situation is essential considering environmental, access, and ease of use concerns.
- Serialized IDs assigned to specific assets can eliminate errors in field service and supply chain applications. One ID per asset limits errors and with NFC and QR codes makes a cellular device all the necessary equipment for system communication.